Product Code: ICA13_404
Numerical Simulation of a Combined Welding-Brazing Process. Application to an Aluminum-Titanium Heterogeneous Assembly
Authors:
Morgan Dal, Pimm, Umr 8006 Cnrs - Arts Et Metiers Paristech; Paris France
Patrice Peyre, PIMM Laboratory (CNRS), Ecole Nationale Superieure d'Arts et Metiers; Paris France
Presented at ICALEO 2013
In this study, an heterogeneous Ti/Al assembly is proposed for the built of aircraft structures. This kind of structure combines advantages of both materials: the aluminum is light-weight and less expensive whereas the titanium offers superior mechanical properties. A welding/brazing assembly in overlap configuration is studied. The two materials are the aluminum alloy Al5754 and the quasi-pure titanium Ti40. The aluminum is fused by laser on titanium (solid) and the joining is obtained by the formation of a ceramic intermetallic compound (TiAl3) along the Ti/Al interface (Figure 2). The size of the intermetallic layer has a significant effect on the mechanical strength of the assembly.
The effects of process parameters on the geometrical properties of the assembly are investigated by numerical simulation (finite element method) and experimental validation. More precisely, the effects of the thermal field and of the fluid flow are correlated to the size of the intermetallic layer in an axisymmetric particular case.
The numerical problem is implemented with the commercial software Comsol Multiphysics™, by coupling heat equation, Navier-Stokes equation and the free boundary motion. The latter is treated with the Arbitrary Lagragian Eulerian method and with a particular focus on the contact angle implementation. An experimental validation of the model is realized with a TRUEDISK 10002 laser.
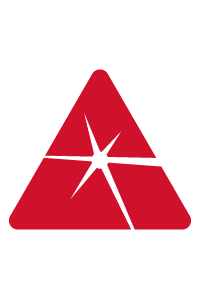
$28.00
Members: $28.00
Note: When applicable, multiple quantity discounts are applied once the items are added to your cart.