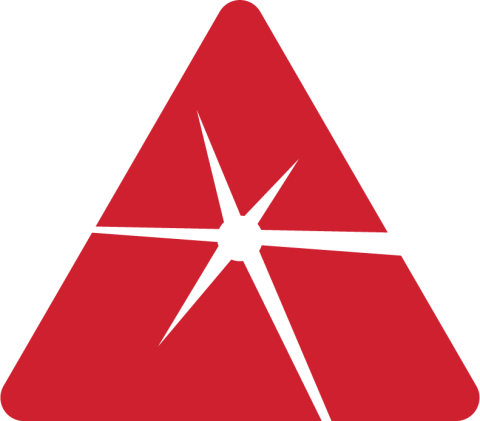
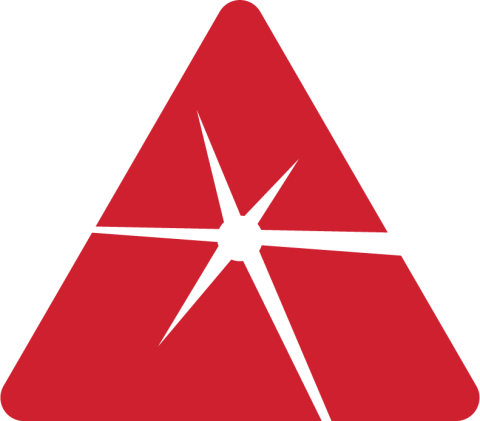
Authors:
M. Naveed Ahsan
Laser Processing Research Centre, School of Mechanical, Aerospace and Civil Engineering, University of Manchester, Sackville Street, Manchester M13 9PL, United Kingdom
Robert Bradley
Henry Moseley X-ray Imaging Facility, School of Materials, University of Manchester, Grosvenor Street, Manchester M13 9PL, United Kingdom
Andrew J. Pinkerton
Laser Processing Research Centre, School of Mechanical, Aerospace and Civil Engineering, University of Manchester, Sackville Street, Manchester M13 9PL, United Kingdom
Laser direct metal deposition has wide application in the areas of rapid manufacturing, surface coating, and component repair. Defects of interlayer and intralayer porosity are often observed in laser deposited structures and repaired components. Interlayer porosity can be controlled to some extent by adjusting processing parameters, but there is still disagreement as to the source of intralayer porosity and whether process conditions, process parameters, or initial powder materials are the dominant causal factor. In this work, two samples of Ti–6Al–4V powder, prepared using gas-atomization and the plasma rotating electrode (PREP) process, were analyzed using laser diffraction and microcomputed tomography for any initial porosity content. A 1.5 kW diode laser with a coaxial deposition head was then used to deposit a number of thin-wall structures with the different powders at different processing parameters. The deposited structures were characterized using scanning electron microscopy and microcomputed tomography. The results show a clear positive relationship between initial power porosity and intralayer porosity in deposition samples. However, the effect of processing parameters is more complex and analysis reveals that other factors such as strong Marangoni flow, pool instability, and the surrounding atmosphere may have an effect. The main trends found are a reduction in porosity with increased power and high porosity at very low mass flow rates; thus, for high value parts, PREP powder, higher power, and moderate powder mass flow rate, as dictated by other process constraints, appears to be a practical combination.