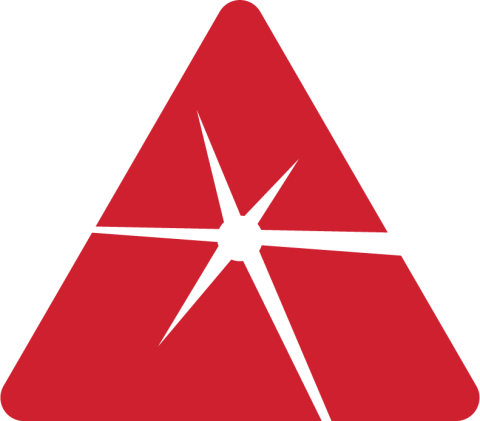
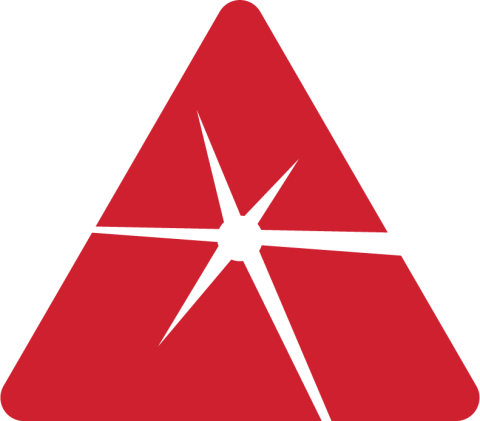
Authors:
Patricia A. I. Popoola
Faculty of Engineering and the Built Environment, Tshwane University of Technology, P.M.B. X680, Pretoria 0001, South Africa
Sisa L. Pityana
Faculty of Engineering and the Built Environment, Tshwane University of Technology, P.M.B. X680, Pretoria 0001, South Africa and Centre for Scientific and Industrial Research-National Laser Centre, P.O. Box 395, Pretoria 0001, South Africa
Olawale M. Popoola
Faculty of Engineering and the Built Environment, Tshwane University of Technology, P.M.B X680, Pretoria 0001, South Africa
In real life engineering applications, production of large area coverage is often required especially for preventing material loss and component damage. To enhance such applications, multiple tracklines laser surface alloying of Al/TiB2 was performed to obtain a large area coverage using Nd:YAG laser. The overlap rate was 50%. The characterization of the metal matrix composite was carried out by optical microscopy (OM), scanning electron microscopy (SEM), and x-ray diffraction (XRD). Results indicated that the microstructure consist of high concentration of TiB2 distributed in the solid solution at front zone of the tracks corresponding to the overlapped region while the track centers contain similar microstructure but with lower content of TiB2 as indicated by energy dispersive spectrometry (EDS). This microstructure is basically similar to that of a single alloyed trackline, but with different percentages of TiB2 reinforcement. The measured microhardness of the overlapped sample decreased with about 11.6% compared to that of the single alloyed trackline because of higher content of TiB2. A 42% increase in wear resistance of the overlapped sample was achieved compared to the as-received Al sample. Corrosion behavior of the multiple laser trackline samples was better than the single laser trackline sample and the as-received sample.