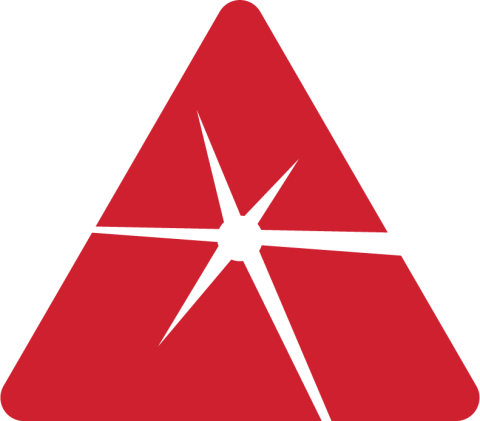
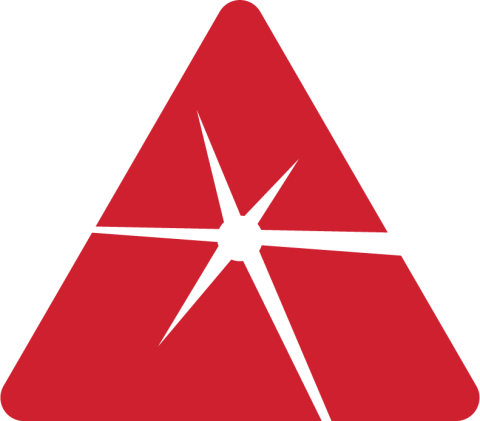
Authors:
Su-Jin Lee
Seiji Katayama
Yousuke Kawahito
Joining and Welding Research Institute, Osaka University, 11-1 Mihogaoka, Ibaraki, Osaka 567-0047, Japan
Keisuke Kinoshita
Vehicle Production Engineering Division, Nissan Motor Co., Ltd., 560-2 Okatsukoku, Atsugi-shi, Kanagawa 243-0192, Japan
Jong-Do Kim
Division of Marine Engineering, Korea Maritime University, Yeongdo-gu, Busan 606-791, South Korea
Zinc-coated steels are widely used in automobile bodies. Laser welding, which offers a lot of advantages over the conventional welding with metal active gas welding, CO2 arc, etc. in terms of improved weld quality, high-speed, and easy automation, has been developed for cars. However, in laser lap welding of zinc-coated steel sheets without gaps, defects such as underfilled beads or porosity were easily formed due to higher pressure of zinc vapor trapped in the molten pool because of the lower boiling point of zinc (1180 K) with respect to the melting point of steel (Fe, 1803 K). Laser lap welding results of two Zn-coated steel sheets have been reported. However, there are not enough data for welding of three Zn-coated steel sheets. Therefore, to understand laser lap weldability of three Zn-coated steel sheets, lap welding of two or three sheets with and without gaps was performed using 16 kW disk laser apparatus with a scanner head, and molten pool motions, spattering, and keyhole behavior during welding were observed by high-speed video cameras and x-ray transmission real-time imaging apparatus. Lap welding of three steel sheets was difficult but acceptably good welds were produced in sheets with upper and lower gaps of 0.1 and 0.1 mm, 0.1 and 0.2 mm, or 0.2 and 0.1 mm, respectively. Bubble generation leading to porosity formation was observed, and it was confirmed that welding phenomena were different depending upon the gap levels.