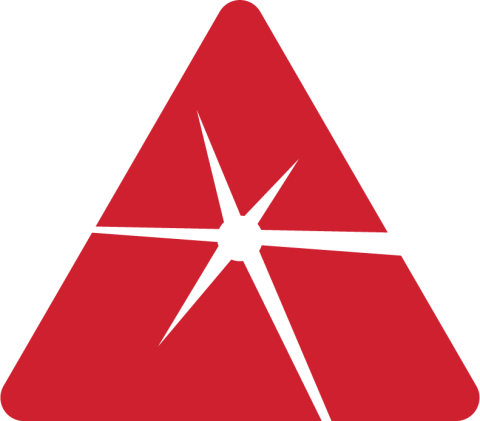
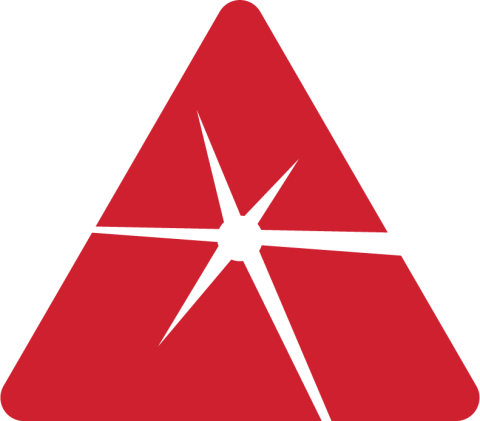
Authors:
L. S. Mayboudi
A. M. Birk
G. Zak
Mechanical and Materials Engineering, Queen’s University, Kingston, Ontario K7L 3N6, Canada
P. J. Bates
Chemistry and Chemical Engineering, Royal Military College, Kingston, Ontario K7K 7B4, Canada
Laser transmission welding (LTW), a technique to join thermoplastic components, involves a laser beam passing through a laser-transmitting part and then being absorbed by the laser-absorbing part at the weld interface. To form a strong bond, it is important that the weld interface be exposed to sufficient heat to melt the polymer without degrading it. A lap-joint geometry was investigated and the interaction between a stationary laser beam and the plastic was observed using a thermal imaging camera. Several coatings on the surface observed by the camera were evaluated. Time histories and temperature distribution on the sample surface transverse to the joint interface were obtained. Soot-coated surface was found to heat up in response to the scattered laser light, providing means for estimation of the scattered light intensity. The LTW welding process was modeled in three dimensions using a commercial finite element solver. This thermal model addresses the heating and cooling stages in a laser welding process in detail, including the effects of laser beam profile and laser beam scattering in a semicrystalline material. The model matched well the temperature distributions obtained by thermal imaging observations on the laser-absorbing part.