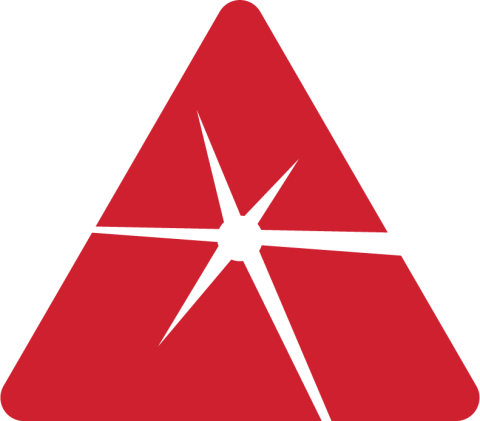
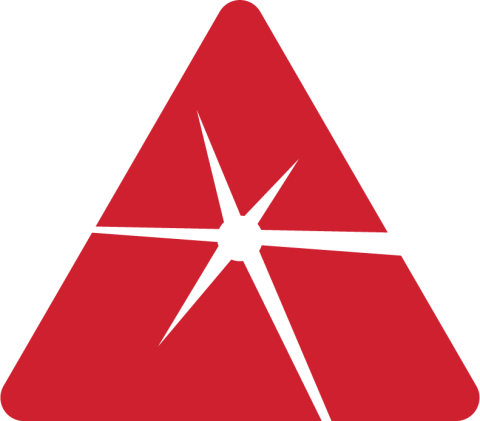
Authors:
Hongping Gu
Boris Shulkin
Stronach Centre for Innovation Magna International Inc., Aurora, Ontario, Canada L4G 7L6
The humping effect in laser beam welding has long been recognized as an adverse effect that limits the achievable welding speed in high power laser beam welding applications. By nature, this effect results in a rough weld bead in laser beam welding and affects the weld integrity. In the past, efforts have been made to suppress the humping effect in laser welding. However, it has been found that the humping effect can have a practical use during the preprocess stage for generating “dimples” for laser beam lap welding of zinc coated sheet metals. Remote laser welding takes advantage of less mechanical movement and better accessibility of the beam to the workpiece, thus fast processing speed can be achieved. Furthermore, currently remote laser welding is mostly suitable for lap joints. However, laser beam lap welding of zinc coated steel components is not a straightforward process and it requires a special procedure to provide proper venting for the zinc vapor which is generated in the interface during welding. Laser dimpling appears to be one of the most efficient and practical methods to produce localized gap for venting zinc vapor during welding. Laser dimpling can be achieved using a moving laser pulse at a typical welding speed. Due to its high speed phenomenon, the humping effect is an ideal high-speed process to generate dimples. It has been demonstrated that the humping effect is a cost effective method to be used in a preprocess stage for remote laser lap welding of zinc coated sheet metals.