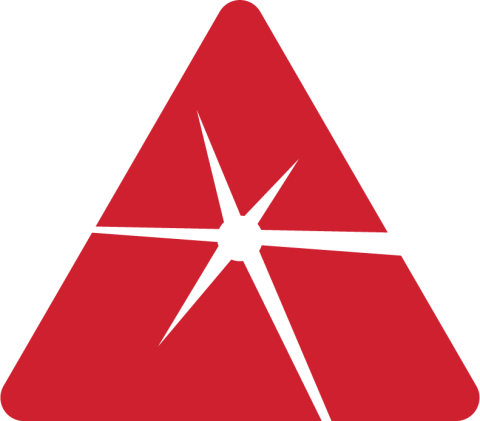
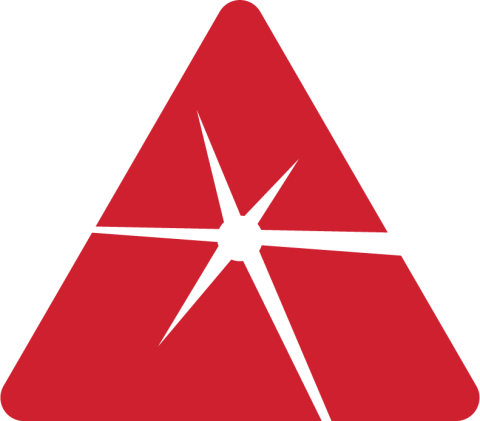
Authors:
Khai Xuan Pham
Rie Tanabe
Yoshiro Ito
Department of Mechanical Engineering, Nagaoka University of Technology, 1603-1 Kamitomioka, Nagaoka, Niigata 940-2188, Japan
Microholes of 100–300 µm diameters were trepanned on cemented tungsten carbide plates of 0.5 and 1 mm thicknesses by means of femtosecond laser pulses using a galvano-scanner with an f-θ lens of 80 mm focal length. It was found that the focus position of the laser beam relative to the sample surface affects the drilled hole shape and drilling speed. Focus on the surface produced a less tapered hole and a higher machining speed than focus 0.5 mm away from the surface in either direction. A low scan speed of the laser beam of 0.035 mm/s produced straighter, less tapered, and more symmetric holes than a high scan speed of 15 mm/s. However, the high scan speed resulted in a higher machining speed. A circular polarized beam resulted in round holes, whereas a linearly polarized beam produced distortions in the shape of the holes. It was also found that laser-induced periodic surface structures with a period of 300 nm were formed on the entire side surface of the holes drilled using circularly polarized beam. The formation of pores on the side walls of the drilled holes was observed and considered as the selective removal of cobalt.