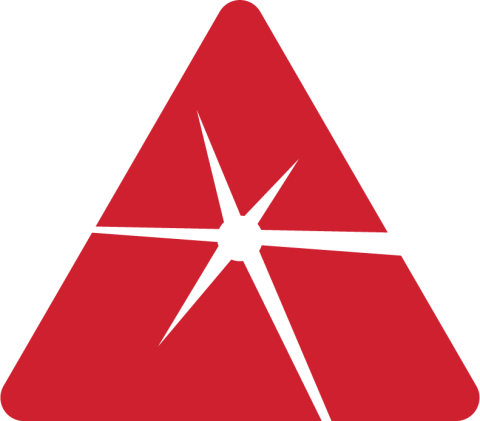
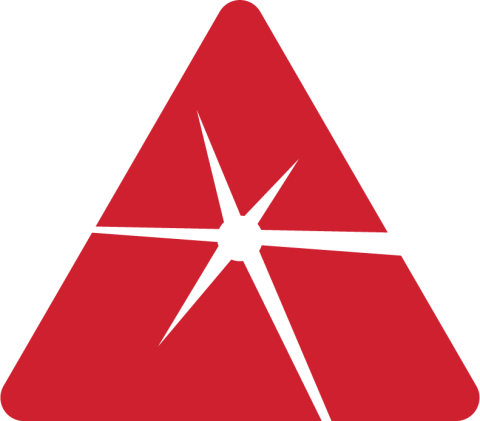
Authors:
Marleen Rombouts
Gert Maes
Myrjam Mertens
Willy Hendrix
VITO, Vlaamse Instelling voor Technologisch Onderzoek, Department of Materials Technology, Boeretang 200, 2400 Mol, Belgium
Laser metal deposition (LMD) is used in industry to coat, additive manufacture, and/or repair high value metal components through deposition and laser induced melting of powder delivered in a gas stream. This study relates to the production of three-dimensional Inconel 625 components by LMD. After LMD, a dense cellular – dendritic structure containing carbides of the type MC, M23C6, and M6C has been detected by x-ray diffraction. Parts with tensile yield strengths, ultimate strengths, and elongations in the range of, respectively, 480–656 MPa, 882–1000 MPa, and 24%–36% have been obtained. Compression testing along and perpendicular to the build direction reveals a slight anisotropy in fracture strength. This is attributed to the preferential orientation of the dendrites parallel to the build direction. Tensile test samples have been fabricated in “lying” and “standing” orientations. The tensile yield and ultimate strength are considerably lower and the elongation is larger for the samples built in standing orientation compared to those built in lying orientation. The tensile properties are affected both by the tensile loading orientation relative to the build orientation and the difference in cooling rate for the two build geometries. The former effect is related to the anisotropic microstructure after LMD. The impact of build geometry on the other hand results in a coarser microstructure and different phase constitution—including larger amount of carbides—in the standing oriented samples due to the lower cooling rate during LMD compared to the lying oriented samples.