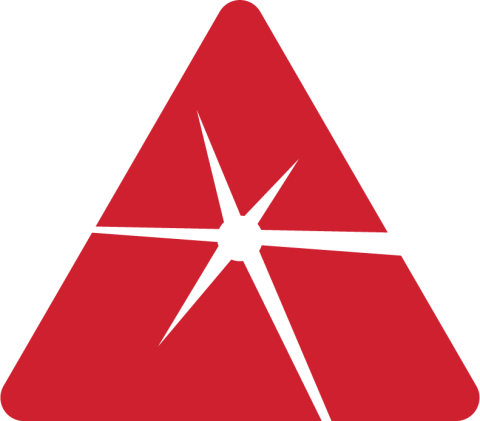
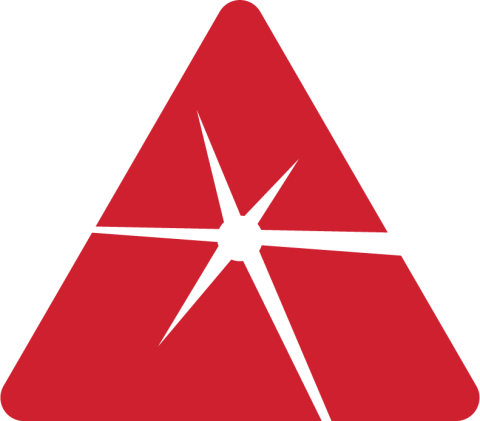
Authors:
XuanTuoi Do
State Key Laboratory for Manufacturing Systems Engineering, Xi'an Jiaotong University, No. 28, Xianning West Road, Xi'an 710049, China and Le Quy Don University, No. 100, Hoang Quoc Viet Street, Hanoi 7EN-218, Vietnam
Dichen Li
Anfeng Zhang
Bin He
Haiyang Zhang
State Key Laboratory for Manufacturing Systems Engineering, Xi'an Jiaotong University, No. 28, Xianning West Road, Xi'an 710049, China
Tatkhoa Doan
State Key Laboratory for Manufacturing Systems Engineering, Xi'an Jiaotong University, No. 28, Xianning West Road, Xi'an 710049, China and Le Quy Don Technical University, No. 100, Hoang Quoc Viet Street, Hanoi 7EN-241, Vietnam
Direct laser forming has the advantage that the heat input is very much localized and it leads to large temperature gradient. Therefore, the solidification velocity can be controlled to stabilize the columnar crystal growth and to avoid the growth of equiaxed grains in the laser clad. Consequently, single crystal can be deposited onto a single crystal substrate. In this paper, DZ125L Ni based super-alloy was used for the experiment, the epitaxial growth of columnar crystal onto the substrate was characterized, and the epitaxial growth of columnar crystal in multi-track multi-layer deposition was obtained by analyzing the single cladding track characteristics and optimizing the technological parameters. The investigation is helpful for the approach to form 3D metal parts such as turbine blades, which require columnar crystal microstructure.