Product Code: ICAL06_308
Laser Percussion Drilling of Aerospace Material
Authors:
Mohammed Naeem, GSI Group, Inc.; Rugby Great Britain
Presented at ICALEO 2006
Aerospace gas turbines require large number small diameter holes (<1mm) to provide cooling in the turbine blades, nozzle guide vanes, combustion chambers and afterburner. Many thousands of holes are introduced in the surface of these components to allow a film of cooling air to flow over the component. Film cooling both extends the life of the component and enables extra performance to be achieved from the engine. Drilling these holes by pulsed Nd: YAG laser is now well established. Such holes can be successfully produced by laser trepanning, but this is relatively slow process compared with laser percussion drilling. Both these drilling techniques are currently performed using direct free space mirror delivery system. The aerospace industry would like to move a fiber delivery system because laser drilling via an optical fiber can offer a number of advantages i.e. -An optical fiber laser beam delivery system offers the option of standardising the beam path for all CNC machines. -Optical fibres homogenise the power distribution across the laser beam giving a top hat profile. -An optical fibre allows the use of beam sharing optical components so that a aerospace component of the right geometry can be drilled in either of two configurations. This paper investigates laser percussion drilling with a high peak power laser (up to 22kW) fitted a 300µm fiber. Holes were drilled with various laser and processing parameters on coated and uncoated nickel based superalloy to quantify recast layer, taper, oxidized layer and cracking.
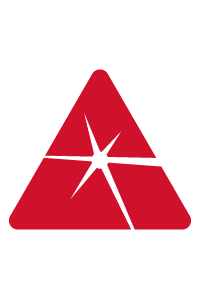
$28.00
Members: $28.00
Note: When applicable, multiple quantity discounts are applied once the items are added to your cart.