Product Code: ICAL08_1902
Laser Shock Processing of 6056 Aluminium Alloy and Influence of the Overlapping Rate: 3D Modelling and Experimental Validation
Authors:
Hongbin Song, Lim-Ensam, Umr 8006 Cnrs; Paris France
Patrice Peyre, Lalp-Gerailp, Upr 1578 Cnrs; Arcueil France
Herve Pelletier, Lgeco, Ea 3938, Insa De Strasbourg; Strasbourg France
Vincent Ji, Icmmo/Lemhe, Umr Cnrs 8182; Orsay France
Vincent Vignal, ICB, UMR5209, Cnrs; Dijon France
Olivier Heintz, ICB, UMR5209, Cnrs; Dijon France
Presented at ICALEO 2008
6056 aluminium alloy is a well-known aeronautical alloys with numerous applications such as fuselage of civil aircrafts. To preserve its surface integrity and protect from fatigue, pitting corrosion or fatigue-corrosion damage, laser-shock processing (LSP) is a serious candidate versus conventional surface treatments (shot-peening). Following previous 2D investigations, a three-dimensional finite element model was implemented on ABAQUS 6.5 explicit to predict residual stresses and deformations induced by various LSP onditions, starting from the prediction of one single impact (2 mm diameter), before addressing the case of a 5 x 5 = 25 impacts condition with various overlapping rates (25 %, 50 % and 67 %). The major issue for LSP modelling is to address both a very high strain rate loading (106 s-1) and a long relaxation time to reach a quasi-residual state. For this, a preliminary step was carried out to optimise : (1) boundary conditions (with or without infinite elements), (2) possible damping conditions (to attenuate shock waves oscillations), (3) time increments (by reducing the automatic time increment provided by ABAQUS), (4) time between subsequent impacts. Simulations were confronted to residual stress determinations by conventional and grazing incidence x-ray diffraction experiments and evidenced that : (1) the global surface heterogeneity and its dependence versus overlapping rate could be successfully addressed by simulations, (2) the surface deformations (in µm) are rather well reproduced by simulations, (2) the simulated residual stress profile exhibit a sub-surface maximum stress which differs from experimental data. Last, new materials behaviours are proposed for improving the mechanical modelling.
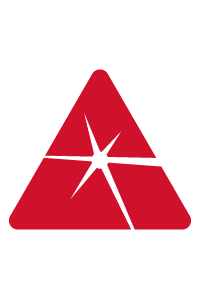
$28.00
Members: $28.00
Note: When applicable, multiple quantity discounts are applied once the items are added to your cart.