Product Code: ICAL09_1002
Direct Fabrication of a Ti-47Al-2Cr-2Nb Alloy by Selective Laser Melting and Direct Metal Deposition Processes
Authors:
Christophe Colin, Centre Des Materiaux, Mines Paris, Paristech; Evry France
Ludovic Thivillon, Enise; Saint-Etienne France
Marc Thomas, Onera; Chatillon France
PASCAL AUBRY, CEA; Gif-sur-Yvette France
Patrice Peyre, Arts Et Miers Paristech; Paris France
Philippe Bertrand, Enise; Saint-Etienne France
Thierry Malot, Arts Et Miers Paristech; Paris France
Thomas Vilaro, Centre Des Materiaux, Mines Paristech; Evry France
Vera Kottman-Rexerodt, Onera; Chatillon France
Vincent Ji, Arts Et Miers Paristech; Paris France
Presented at ICALEO 2009
A Ti-47Al-2Cr-2Nb (at.%) material was fabricated using two laser-based methods, Selective Laser Melting (SLM) and Direct Metal Deposition (DMD), for potential uses in aircraft jet engines. Experiments were conducted under controlled atmosphere by changing the following processing parameters : starting powder size, laser power, powder feeding rate, laser scanning direction, deposit rate, pre-heat temperature. Optimal parameters were used with this relatively low ductility material to prevent cracking due to built-up residual stresses during fast cooling. It was observed that these non-equilibrium fast-cooling conditions hinder the formation of ultra-fine, Widmanstätten or massive transformation structures. Accordingly, the high microhardness value obtained in the layer by layer deposits were attributed to refined and metastable structures. Post heat-treatments were successfully used to restore homogeneous lamellar or duplex microstructures and to relieve the residual stress. A comparison of these two methods is provided in terms of powder requirements and of process parameters to achieve un-cracked structures and fully dense materials. Finally, process limitations relative to the microstructures generated and to the domains of application are discussed.
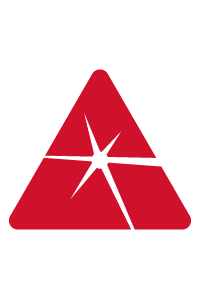
$28.00
Members: $28.00
Note: When applicable, multiple quantity discounts are applied once the items are added to your cart.