Product Code: ICA13_1903
Macro-Structuring of Composite Material by UV-Laser Ablation
Authors:
Hagen Dittmar, Laser Zentrum Hannover e.V.; Hannover Germany
Peter Jaeschke, Laser Zentrum Hannover E.V.; Hannover Germany
Oliver Suttmann, Laser Zentrum Hannover E.V.; Hannover Germany
Ludger Overmeyer, Laser Zentrum Hannover E.V.; Hannover Germany
Presented at ICALEO 2013
Composite materials like carbon fibre reinforced plastics (CFRP) or glass fibre reinforced plastics (GFRP) have been in use by the aviation and wind energy industry for years due to their lightweight benefits. With the automotive industry entering the CFRP market, the demand for a more economic CFRP production will increase as well as the demand for innovative processing technologies. An approach to meet these challenges is the utilisation of laser technology.
Laser machining of fibre reinforced plastics is already gaining more popularity in the automotive and aviation industry mostly due to laser cutting or drilling and laser transmission welding.
Nanosecond(ns)-pulsed UV-lasers are capable of machining both CFRP and GFRP. These materials are already widely used in also huge components in the aviation and wind energy industries and suffer from damages or wear during operation. Therefore, it is necessary to be able to process composite areas of big dimensions. This need for a reliable repair and production post-process will increase as soon as automobiles containing CFRP parts will go into large batch production and enter the market during the months to come.
One step in such a repair chain or post process can be laser macro structuring to prepare damaged surfaces for a composite bonded repair. For a bonded repair it is important that machined areas show sufficient surface roughness for an optimal wettability. For a possible industrial application, a laser macro structuring process needs to be developed, which produces such surfaces within a short processing time.
In this article glass and carbon fibre reinforced epoxy of unidirectional (UD) ply build up will be investigated in terms of processing speed and surface quality. For a given set of laser and processing parameters the pulse overlap will be optimised in order to find the fastest parameter sets, which will provide appropriate surface roughness and best wettability. The surface roughness will be evaluated utilising a confocal microscope, while the wettability will be investigated using contact angle measurements on a goniometer.
These parameter sets will be used to process bonded butt lap joint coupons for sheer strength tests, in order to compare them not only by processing time and surface roughness, but also by their suitability for a bonded repair of composites.
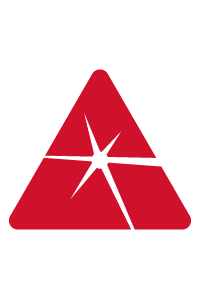
$28.00
Members: $28.00
Note: When applicable, multiple quantity discounts are applied once the items are added to your cart.