Product Code: ICA13_M805
Robusteness of the Laser Melting Process
Authors:
Heiko Bruening, Bias - Bremer Institut Fuer Angewandte Strahltechnik Gmbh; Bremen Germany
Presented at ICALEO 2013
The use of laser technologies in material processing is wide spread in various manufacturing chains such as welding, brazing and cutting. Compared to other heat sources, the laser beam enables the allocation of a certain amount of energy in a specific time on a very small spot. For this reason, the laser especially is a suitable tool for material processing in micro range. Due to the fact that processes in micro range are rather influenced by forces related to the surface of the work piece than by forces related to their volume, a process which is called laser rod end melting can be carried out. In this process the end of a cylindrical, metallic rod with a diameter less than 1.0mm is heated up by a laser beam. The laser beam causes the end of the rod to melt. The molten part directly forms a sphere due to the effect of the surface tension. The size of the preform can be defined by adjusting laser beam power and pulse duration. After cooling, the generated preform can be formed by a mechanical single stage upsetting process. Closed die upsetting necessitates preforms with a well-defined volume as too small preforms would lead to a not completely filled cavity whilst too large preforms would avoid complete closing of dies so that defective forming products are the result.
In this paper results of investigations on the robustness of the laser melting process are presented. The position of the rod relatively to the focus spot and the focus layer is systematically changed to create positioning requirements for the laser melting process. It is shown that the diameter of the preform is influenced by its position relative to the laser spot.
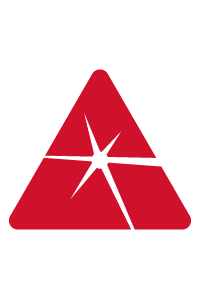
$28.00
Members: $28.00
Note: When applicable, multiple quantity discounts are applied once the items are added to your cart.