Product Code: JLA_21_4_183
Authors:
Boris Regaard
Stefan Kaierle
Reinhart Poprawe
Laser beam welding bears evident advantages regarding precision, quality, productivity, low heat input, and feasibility of automation. At the same time the process calls for high precision of the beam positioning on the workpiece, which therefore imposes high requirements of welding trajectory and feed rate accuracy; e.g., for butt welding the focal point of the laser beam with respect to the joint must be maintained within a typical accuracy better than 20–150 μm, depending on the focused beam radius. To meet these requirements, seam-tracking devices are used. A sensor measures the joint position and computes a correction vector to compensate the joint trajectory offset. The deviation is compensated either by a robot trajectory adjustment or by an additional tracking axis. This paper describes the basic concepts of seam tracking in detail and points out problems in the different control principles, which are evoked by the forerun of the sensor. State-of-the-art sensors and error compensating techniques are presented and analyzed. Further, a new approach for seam tracking is introduced. It uses a multisensor concept, which in addition to the seam position measures the relative displacement between the processing head and the workpiece. An integrated two-dimensional beam positioning system enables “self-guided” processing, which allows high-accuracy tracking of a joint independent of the motion system and disengages from time intensive sensor calibration and robot teaching necessity.
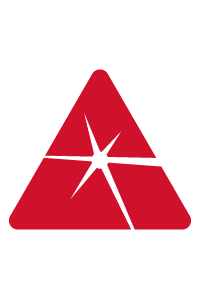
$25.00
Members: $25.00
Note: When applicable, multiple quantity discounts are applied once the items are added to your cart.